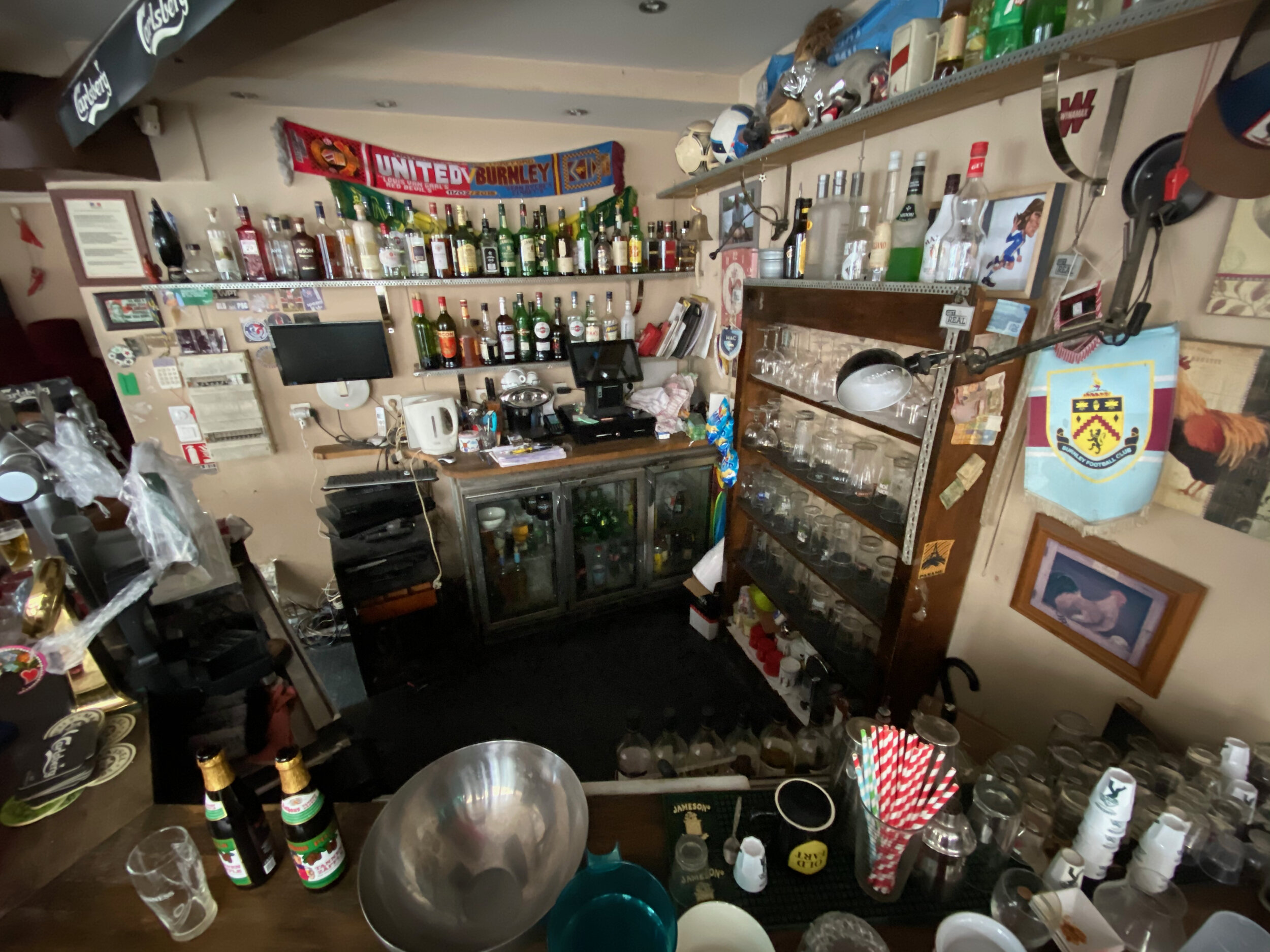
The back bar when it was a mixed collection of temporary fixes. The biggest problem was the audio installation. It was a ramshackle stack of components, unprotected from spilled liquids, with a rat’s nest of wires nearly impossible to maintain. It was also in the way.
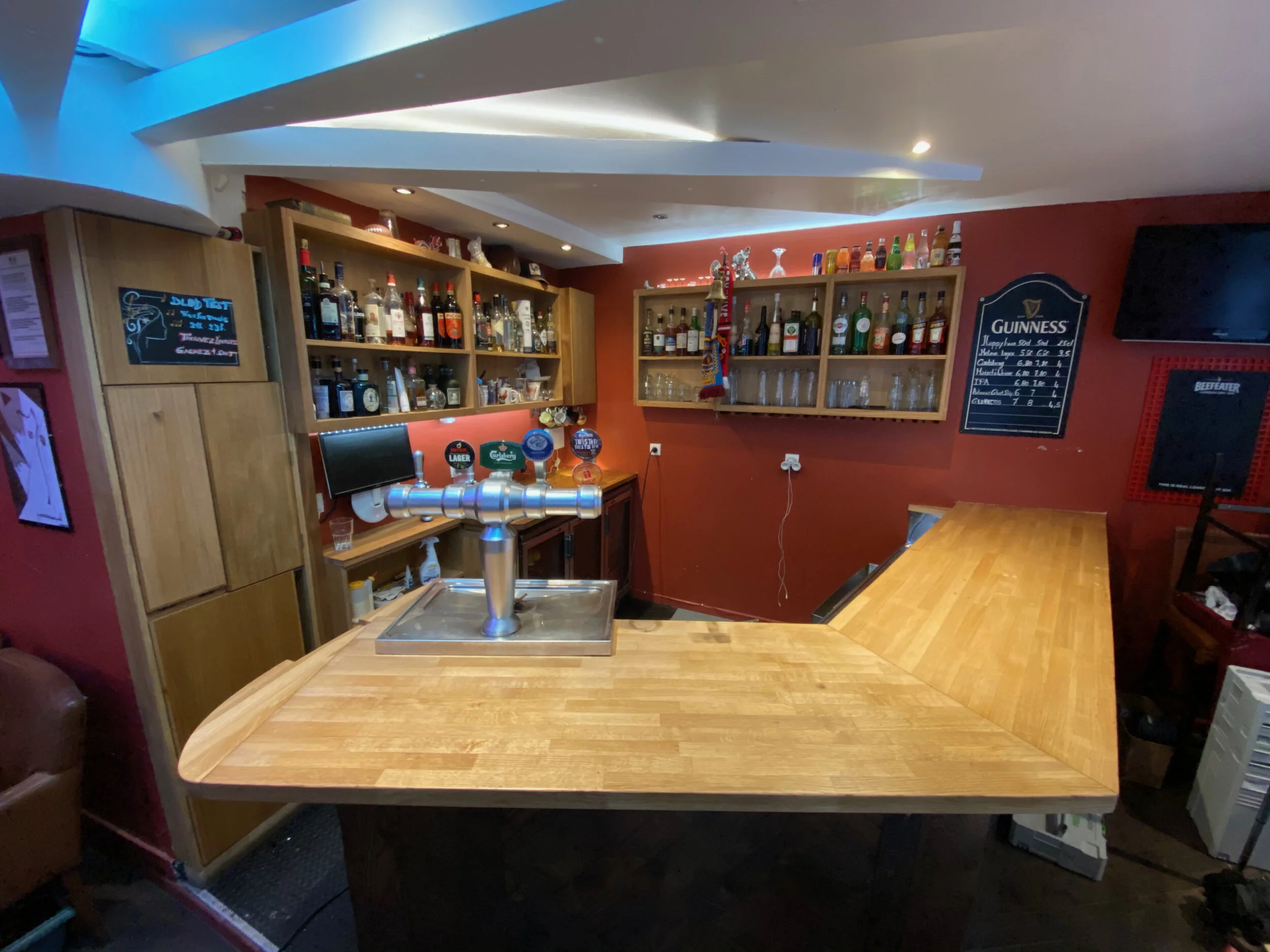
Not part of the original scope, a decision was made to refinish the bar during “reconfinement” — the second lockdown. I was pleased and surprised by the results. A Festool Rotex with progressive grits took care of the old finish (2 stubborn stains at tap locations remain.) Ending at 220 grit before a first coat of oil yielded a baby smooth finish at the 3rd coat, with sanding up to a 400 grit at the end.

Seen before the final details are in place, the space to re-work the back bar was tight. No surprise here in Paris. Balancing a number of needs, a media equipment cabinet impossibly occupies the space at the end of the bar. Why impossibly? All the equipment is mounted flat on the back of a cabinet, on the left of this image, which is only 100mm deep inside.
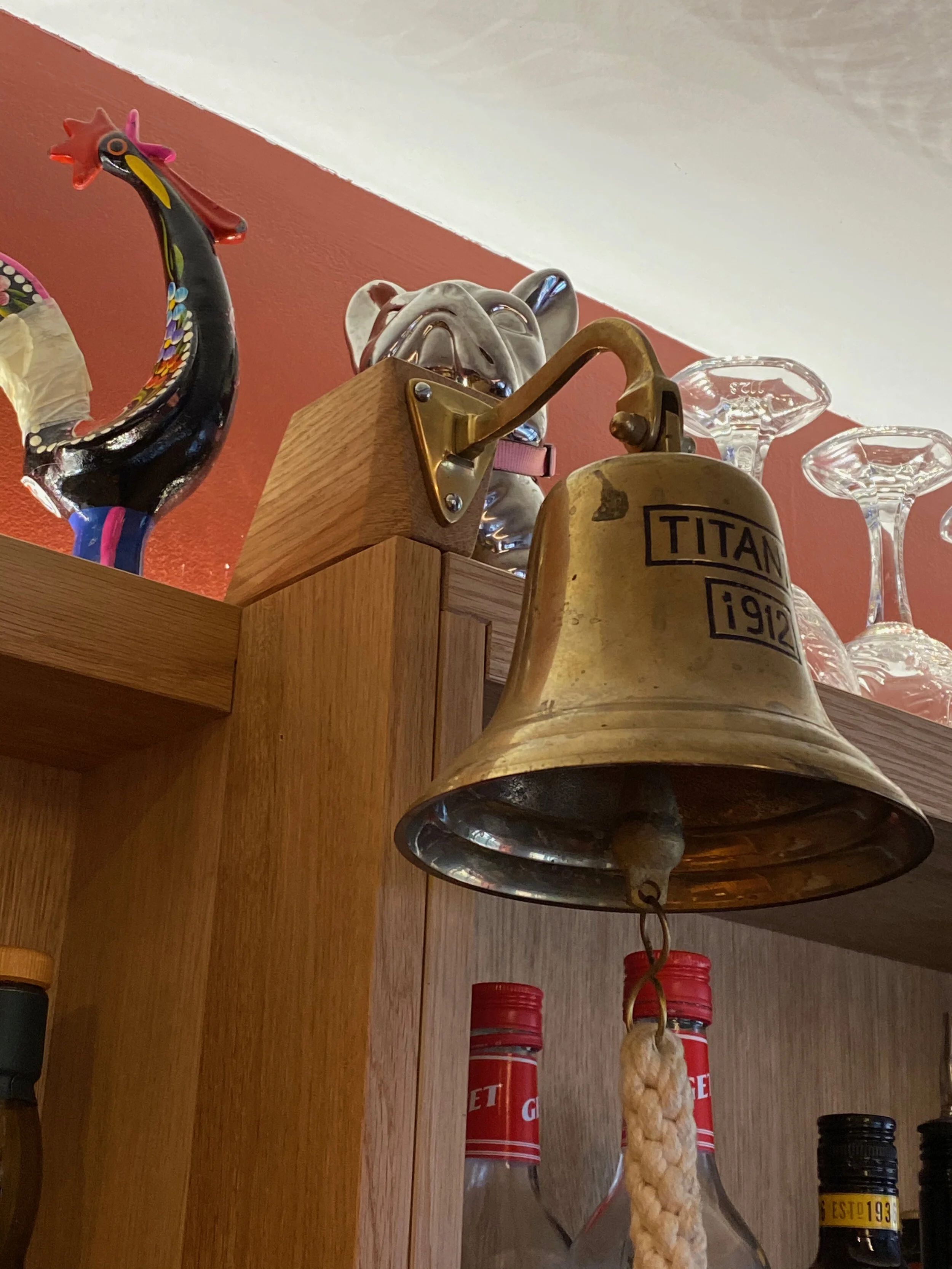
A coq and a bulldog sit alongside the Titanic bell, used to sound last call and bring order to a sometimes raucous bar — or celebrate a win or tip. Added after the design was complete and everything installed, the oak block was shaped to meet the needs of stout attachment and vigorous ringing.

Working with and over the existing cooler proved a challenge. Twice during the work I, with the help of a friend from the pub, emptied and restocked the cooler in order to move it. Working alone at the end, and with just the right amount of blocking in place, I found a way to install trim to give a finished look to the existing cooler. Not handled in this job a large depression in the floor. Shimming the cooler helped with the trim shown here but could do nothing for the scribe required at the end panel to the left.
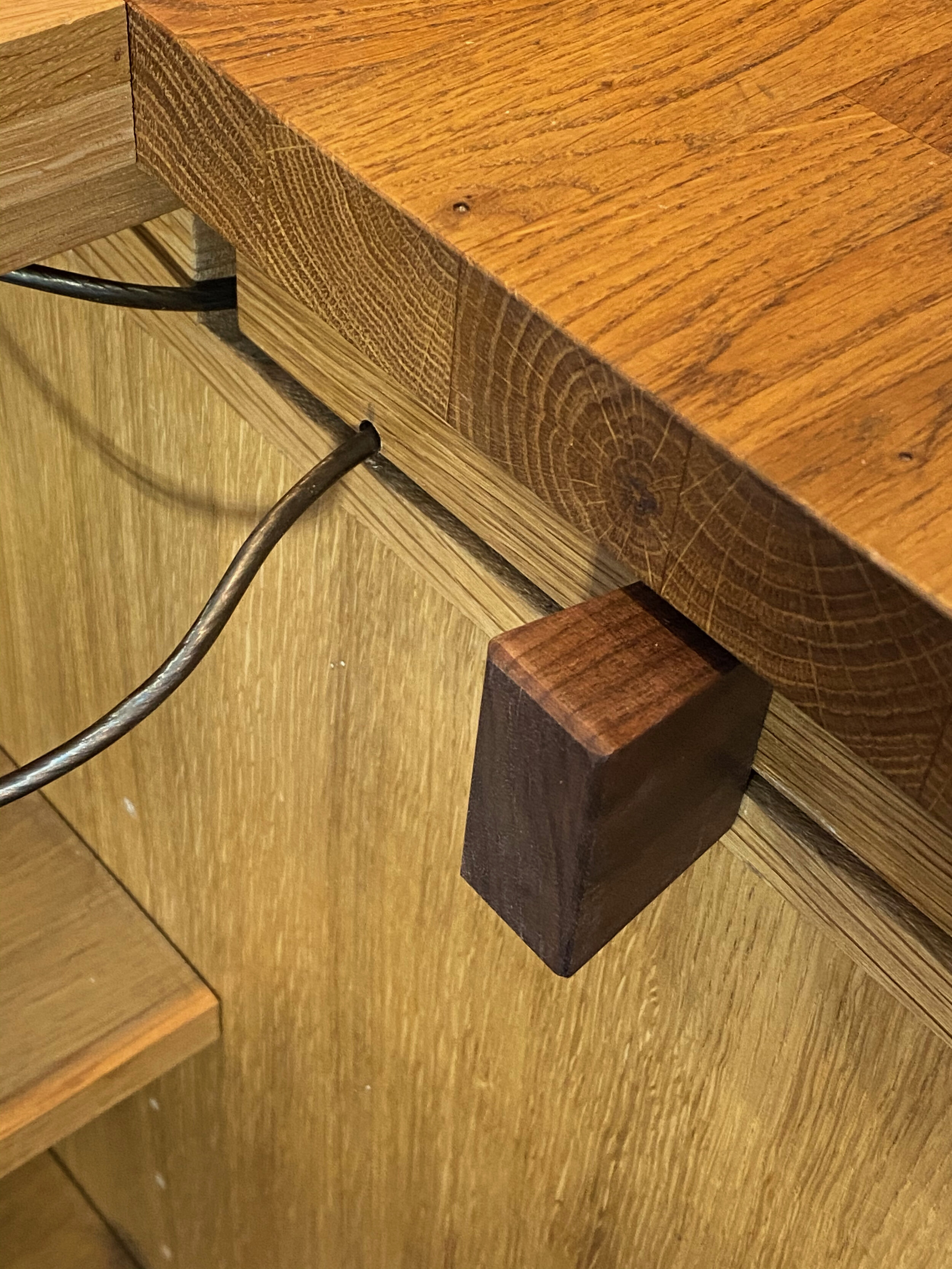
Not without its problems (the wire seen here was thicker and stickier than I imagined), a keyboard tray fits without a millimeter to spare between the work counter and the top of the existing cooler. The pull for the tray was shaped from a scrap of walnut. While a fair amount of material was purchased for this project, I did my best to use what was close as the project moved toward completion and the material purchased ran short.
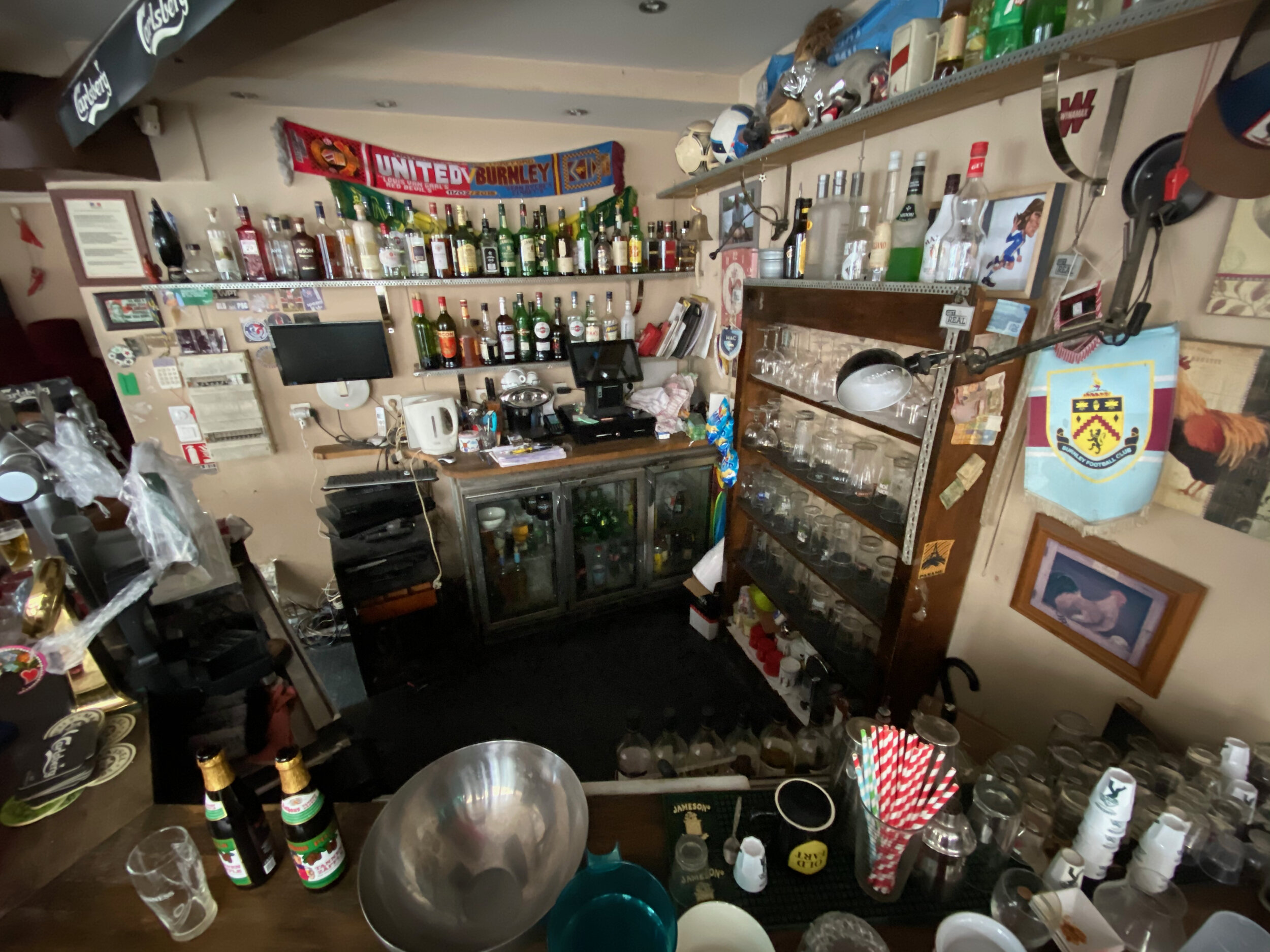
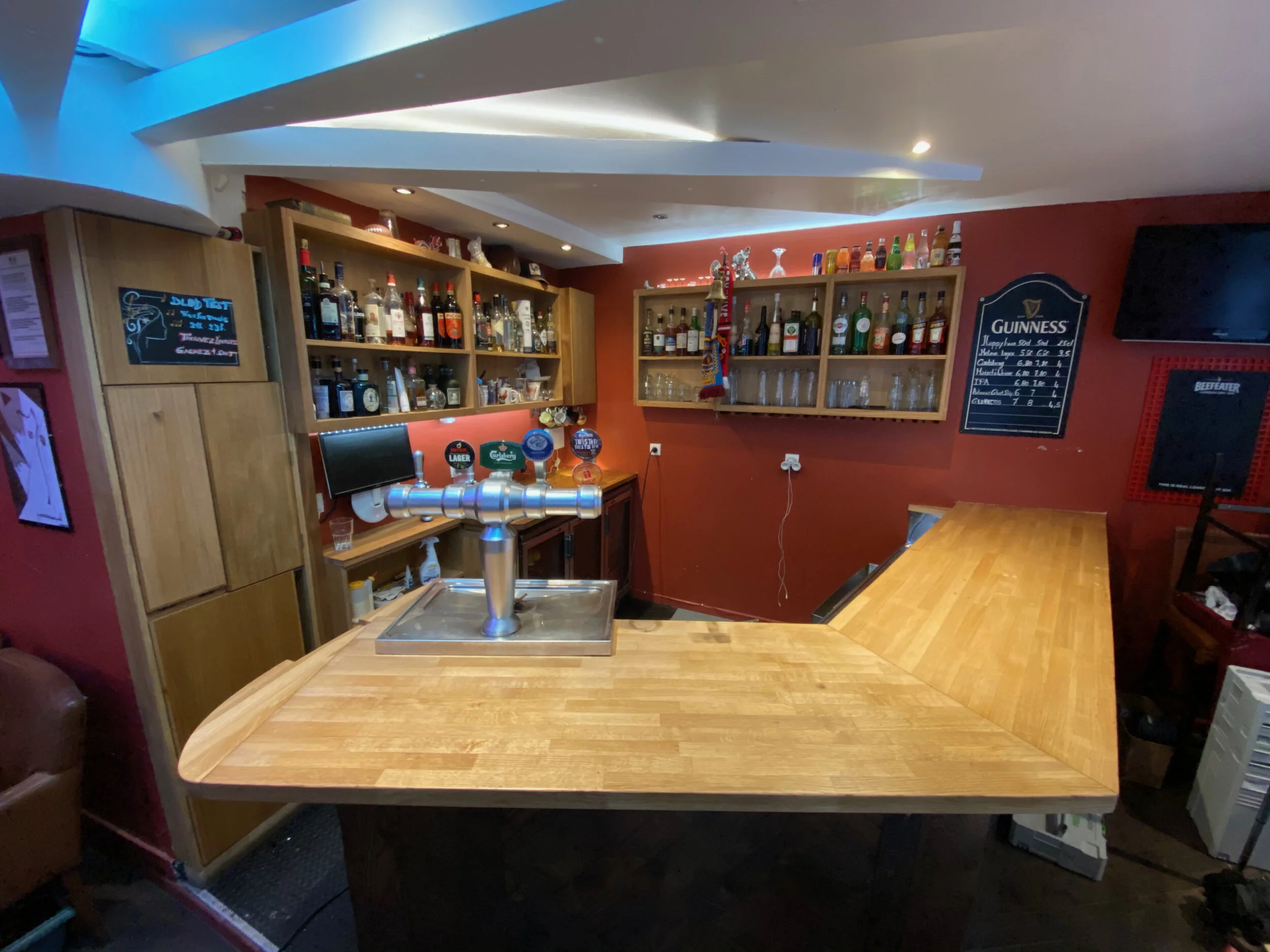

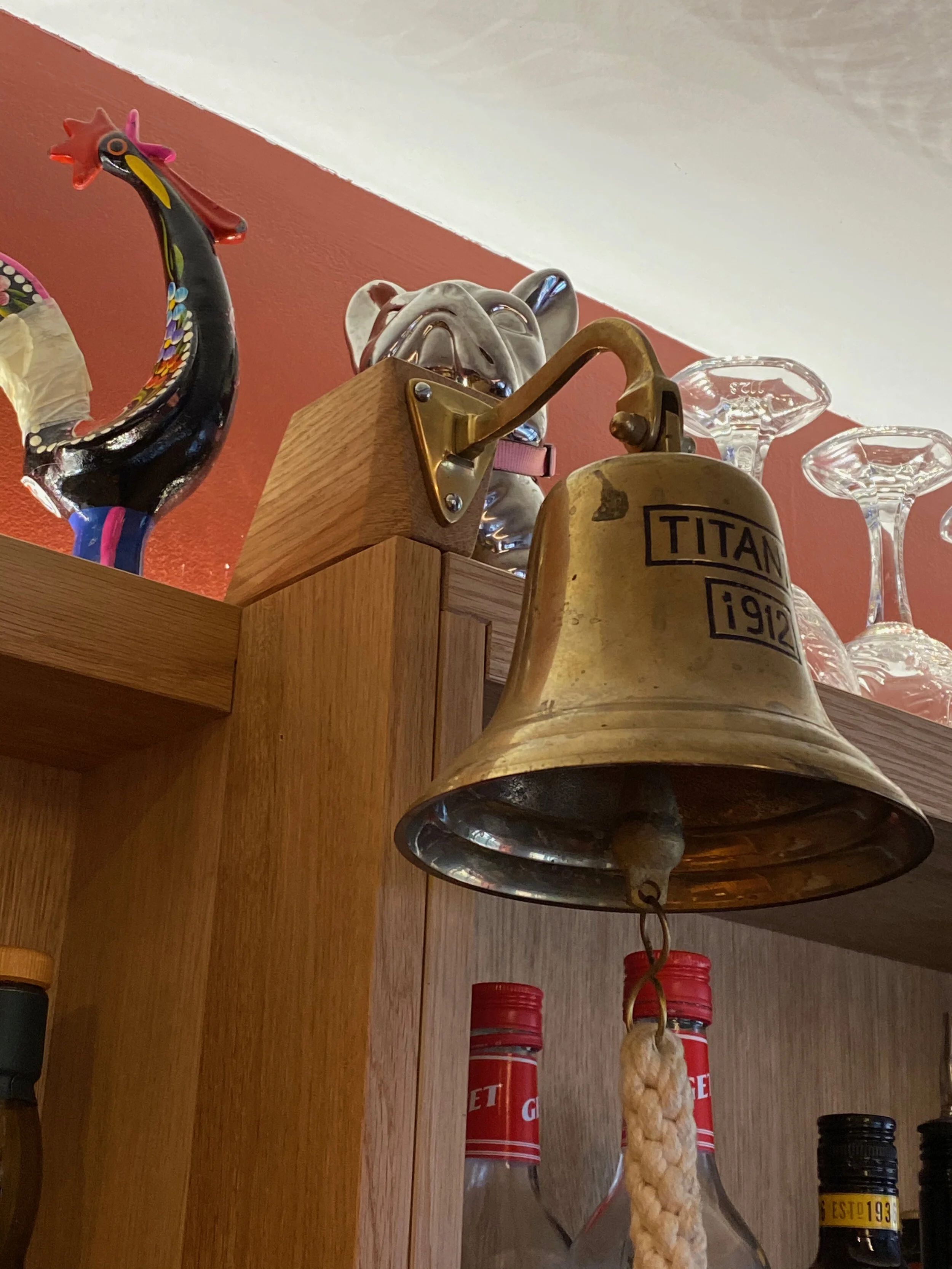

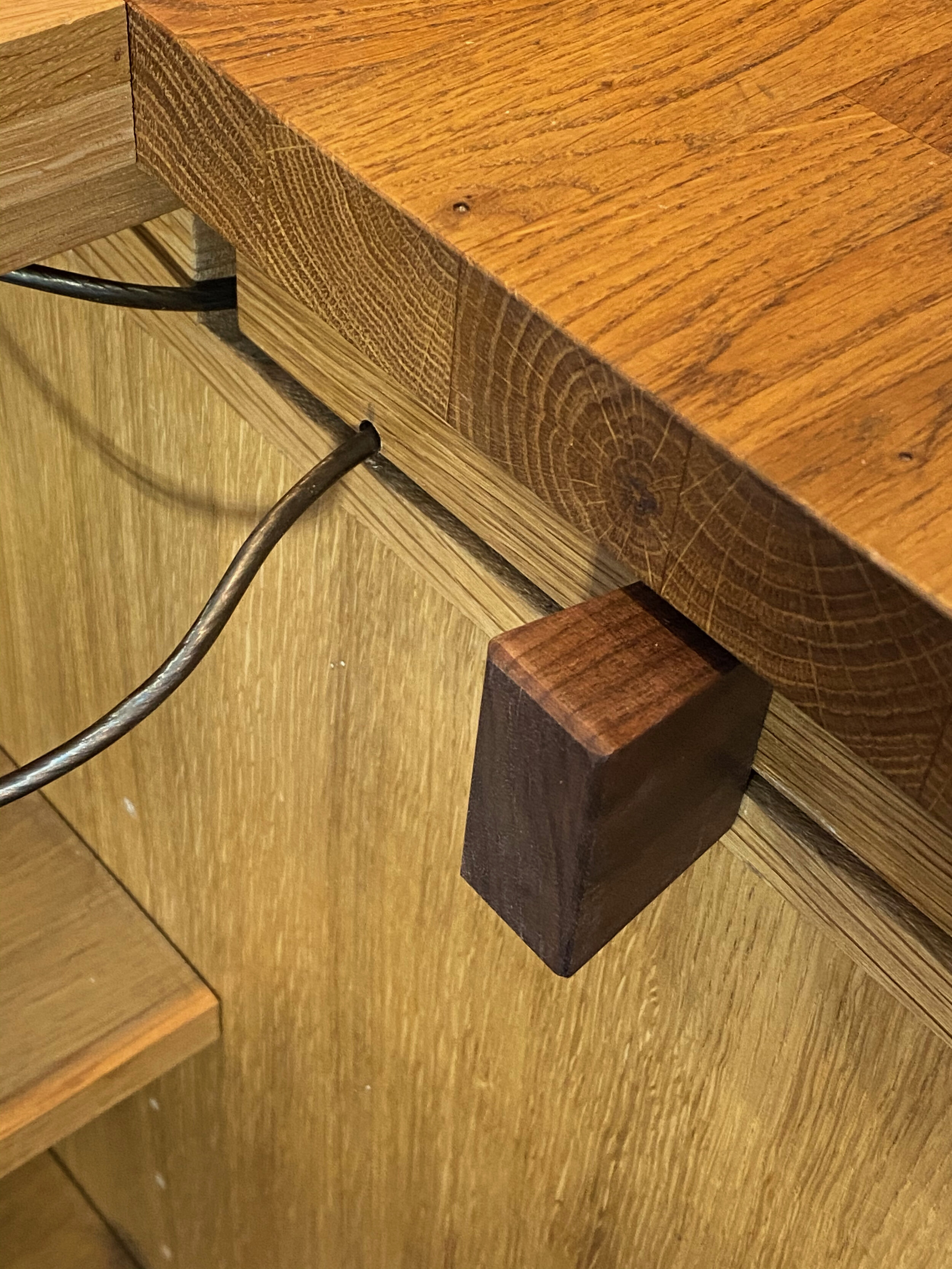
The back bar when it was a mixed collection of temporary fixes. The biggest problem was the audio installation. It was a ramshackle stack of components, unprotected from spilled liquids, with a rat’s nest of wires nearly impossible to maintain. It was also in the way.
Not part of the original scope, a decision was made to refinish the bar during “reconfinement” — the second lockdown. I was pleased and surprised by the results. A Festool Rotex with progressive grits took care of the old finish (2 stubborn stains at tap locations remain.) Ending at 220 grit before a first coat of oil yielded a baby smooth finish at the 3rd coat, with sanding up to a 400 grit at the end.
Seen before the final details are in place, the space to re-work the back bar was tight. No surprise here in Paris. Balancing a number of needs, a media equipment cabinet impossibly occupies the space at the end of the bar. Why impossibly? All the equipment is mounted flat on the back of a cabinet, on the left of this image, which is only 100mm deep inside.
A coq and a bulldog sit alongside the Titanic bell, used to sound last call and bring order to a sometimes raucous bar — or celebrate a win or tip. Added after the design was complete and everything installed, the oak block was shaped to meet the needs of stout attachment and vigorous ringing.
Working with and over the existing cooler proved a challenge. Twice during the work I, with the help of a friend from the pub, emptied and restocked the cooler in order to move it. Working alone at the end, and with just the right amount of blocking in place, I found a way to install trim to give a finished look to the existing cooler. Not handled in this job a large depression in the floor. Shimming the cooler helped with the trim shown here but could do nothing for the scribe required at the end panel to the left.
Not without its problems (the wire seen here was thicker and stickier than I imagined), a keyboard tray fits without a millimeter to spare between the work counter and the top of the existing cooler. The pull for the tray was shaped from a scrap of walnut. While a fair amount of material was purchased for this project, I did my best to use what was close as the project moved toward completion and the material purchased ran short.